Composites – a digital fabrication exhibition made through design
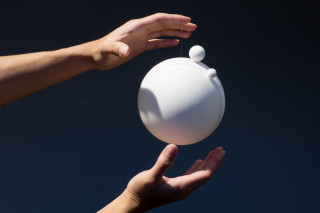
As a part of the elective course ‘digital fabrication technologies and processes’, 13 masters’ design and architecture students have made an exhibition titled Composites. The project, which is hosted by the institute of design and the workshops at AHO, centres on a series of activities, processes and phenomenons which have been investigated with digital fabrication tools and through a designerly framing. Projects include a chair, the concept of time, the fluidity of water, the activities of the playground, paintings, speakers, joinery, post-modernistic reconstruction, the aesthetics of disposable cutlery, and new ways of representing landscape.
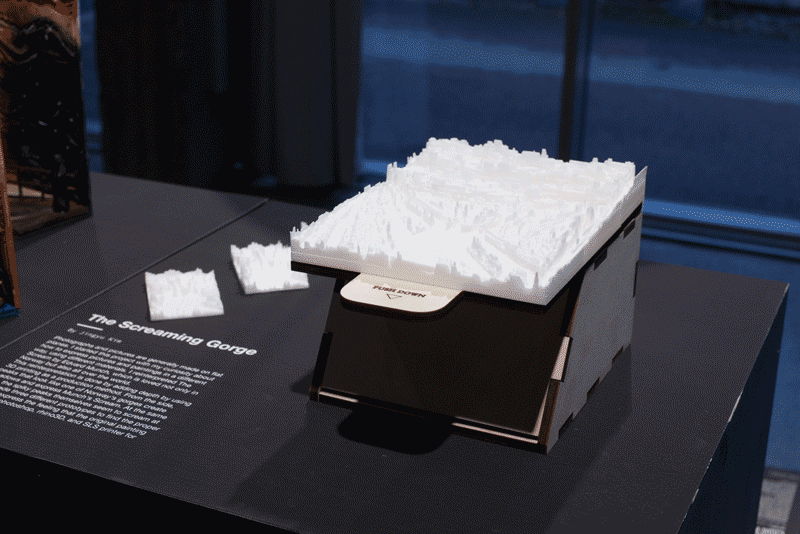
Jingyu Kim – The screaming gorge
Photographs and pictures are generally made on flat planes. I started this project with my curiosity about how to express pictures and paintings in a different way, using different materials. I reinterpreted The Scream by Edvard Munch, which is loved not only in Norway but also all over the world. This reinterpretation is done by adding depth by using 3D printing as a production method. From the side, peaks that look like one of Norway’s gorges create shadows and express Munch’s Scream. At the same time, the spiky peaks themselves seem to scream at us. I made three different prototypes to find the proper depth to express the feeling that the original painting has. I used photoshop, rhino3D, and SLS printer for this project.

Ming Pornchai Paenkhumyat – Time to be seen
Time is an abstract term, but why this picture of the round surface with those hands indicating hour and minute always come to our mind. ‘Time to be seen’ is a design project aimed to give the new aspect of how we can visualise time in the simpliest way. With the same concept, 3 configurations have been made through the different digital fabrication technologies in order to express the characteristics of each. Selective Laser Sintering (SLS) which provide the ability to create the moveable 3D model at once, Laser cutting which has the potential to cut/engrave the surfaces precisely, and with Computer Numerical Control (CNC) milling it is possible to shape the wood by using the CAD file. – SLS – LASER CUTTING – CNC Milling – SLA
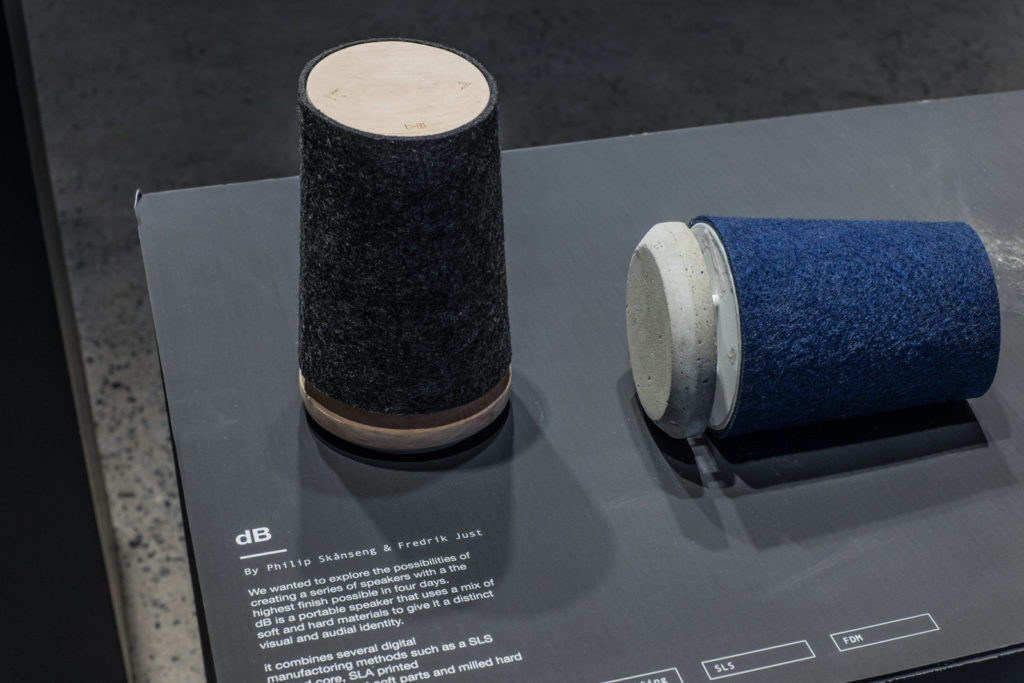
Philip Skånseng & Fredrik Just – dB
dB is a portable speaker that uses a mix of soft and hard materials to give it a distinct visual and audial identity. it combines several digital manufactoring methods such as a SLS printed core, SLA printed details, laser cut soft parts and milled hard parts. – We will showcase three different variations of our speaker, showing that once the digital files have been made, the output can be very different products depending on the materials used. – Tools used: SLS, SLA, FDM, Milling, Laser cutting, silicon moulding and concrete casting.
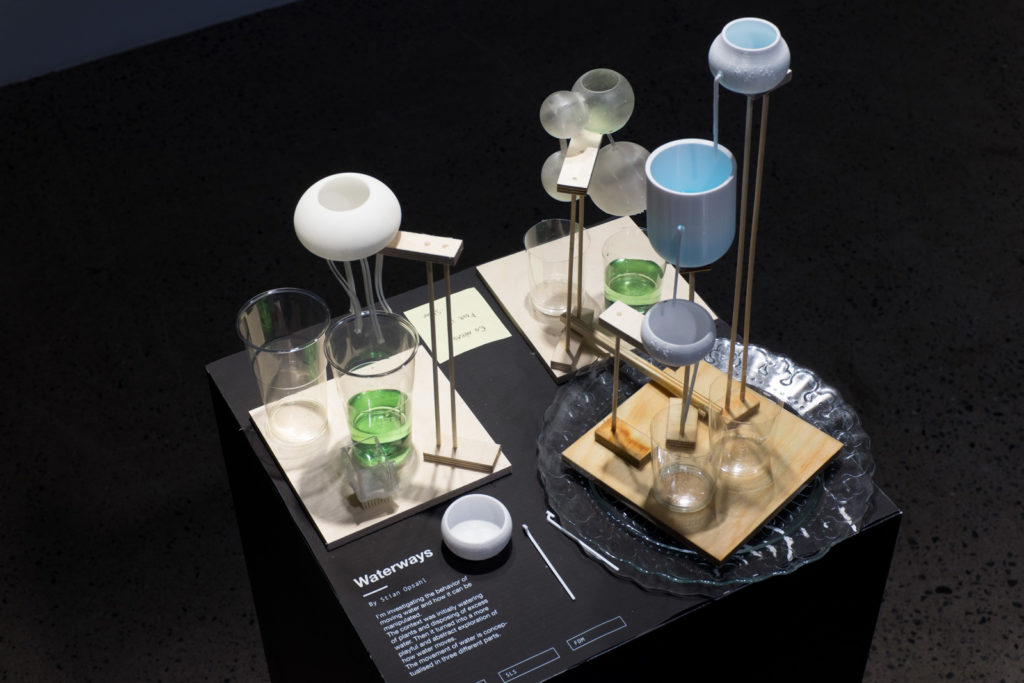
Stian Opsahl – Waterways
I’m investigating the behavior of moving water and how it can be manipulated. The context was initially watering of plants and disposing of excess water. Then it turned into a more playful and abstract exploration of how water moves. The movement of water is conceptualised in three different parts. SLS, SLA, FDM.
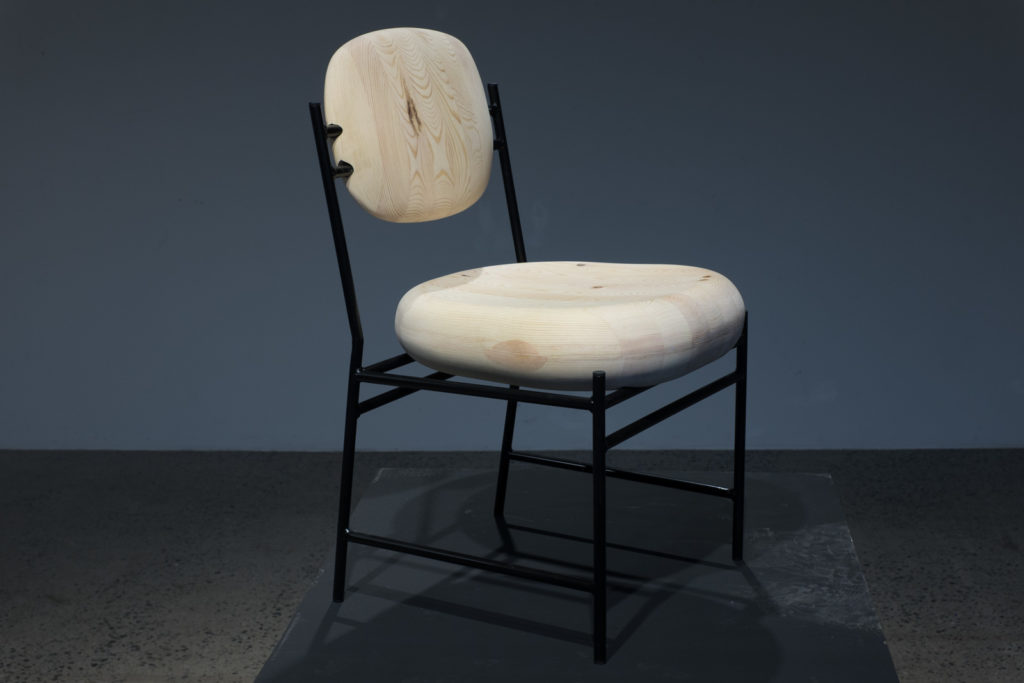
Mikkel Jøraandstad & Tim Cæsar Knutsen – Four Day Chair
How to produce organic, nature-like forms using digital production methods? Trough additive and subtractive manufacturing techniques we are exploring the idea of organic shapes in our chair design. Taking a closer look at how we can use these precise and «robotic» production methods to create objects with a more natural and organic feel. Using the chair as a medium to create a contrast between a rigid frame and the bulging seating we are trying to emphasize the possibilities within these methods.
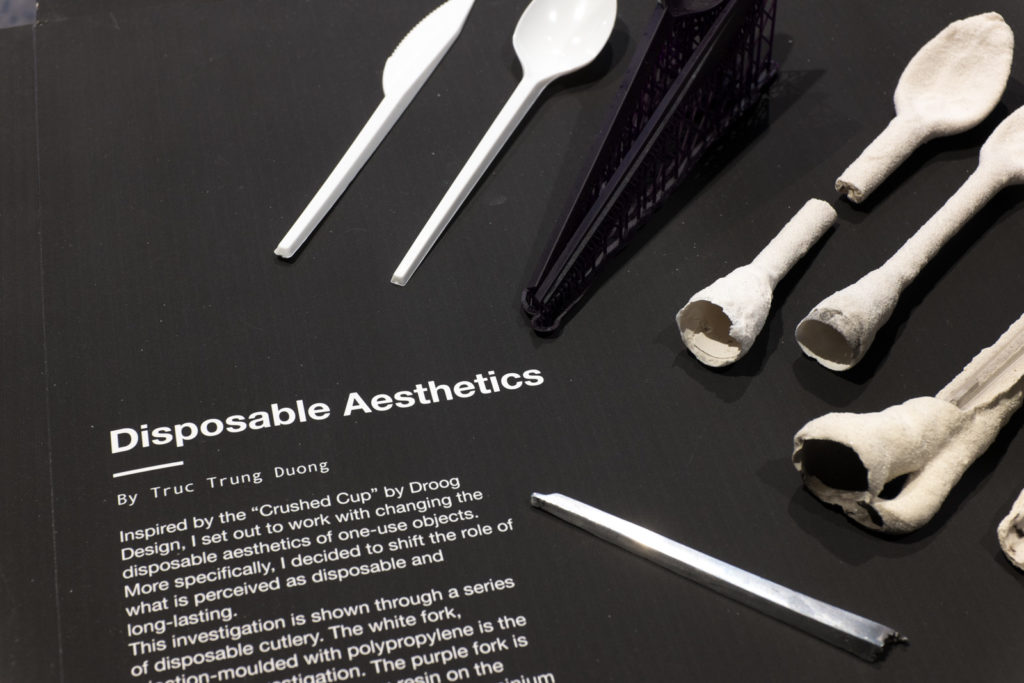
Truc Trung Duong – Disposable Aesthetics
nspired by the “Crushed Cup” by Droog Design, I set out to work with changing the disposable aesthetics of one-use objects. More specifically, I decided to shift the role of what is perceived as disposable and long-lasting. This investigation is shown through a series of disposable cutlery. The white fork, injection-moulded with polypropylene is the base of the investigation. The purple fork is printed with a castable wax resin on the Formlabs Form 2 SLA-printer. The aluminium fork was casted using the printed wax model with the lost wax technique.
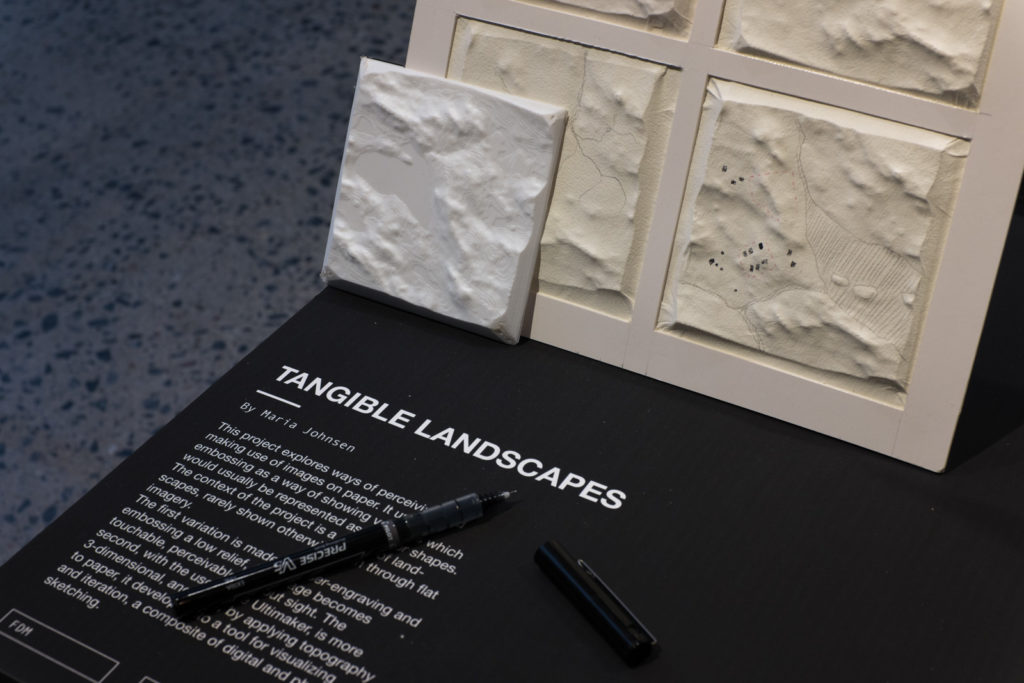
Maria Johnsen – Tangible landscapes
This project explores ways of perceiving and making use of images on paper. It uses embossing as a way of showing volumes which would usually be represented as lines or shapes. The context of the project is a series of landscapes, rarely shown otherwise than through flat imagery. The first variation is made by laser-engraving and embossing a low relief, the image becomes touchable, perceivable without sight. The second, with the use of the Ultimaker, is more 3-dimensional, and third, by applying topography to paper, it develops into a tool for visualizing and iteration, a composite of digital and physical sketching. Laser-cutter and FDM ultimaker
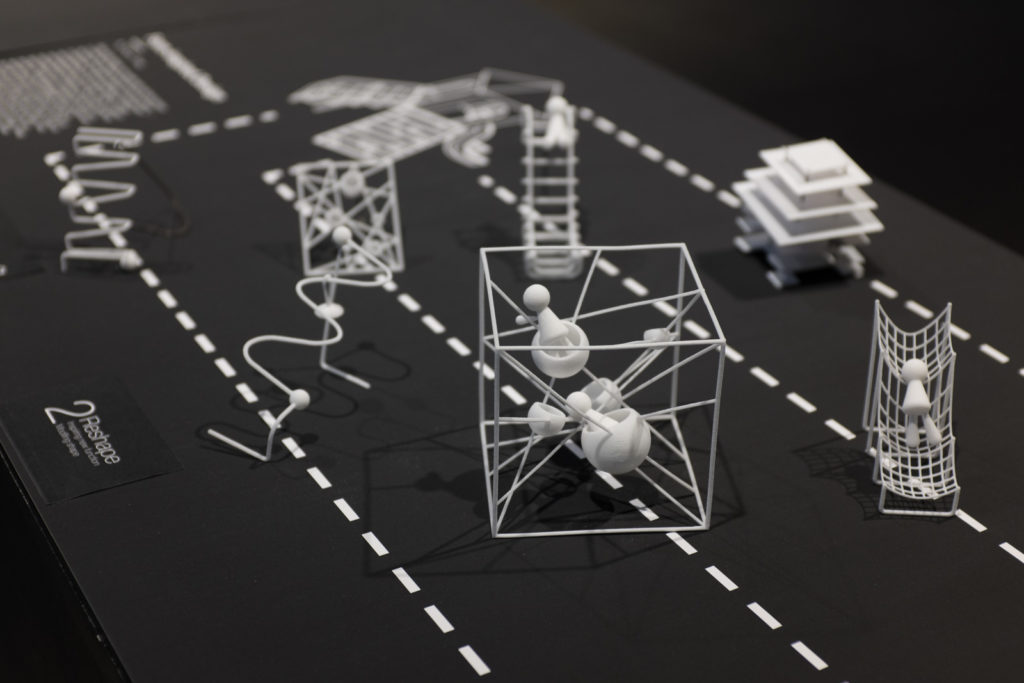
Acy Feng – Form-inspired Design
When doing design, we usually start with the function in mind, then to choose the form which can achieve the function. How about to design in a reversed way? In this project, the “Form-inspired Design”method was experimented in the context of “play” to create a more imaginative playground. The process started by analysing the form of components (tree house is a space, climbing wall is a combination of surface and points, etc.); firstly REFORMING: switching the elements between each components in set order (in this case, point to space, space to surface, surface to line, line to point) with staying the same shape; next, RESHAPING: creating new functions for the new components, and reshaping them accordingly; finally, REASSEMBLING the new component to a whole playground. Form-inspired Design is an exploration of design method, which trying to jump out from a typical design circle and helping designers to engage their imagination and creativity. Please see the prototypes for better understanding . Tools: SLS
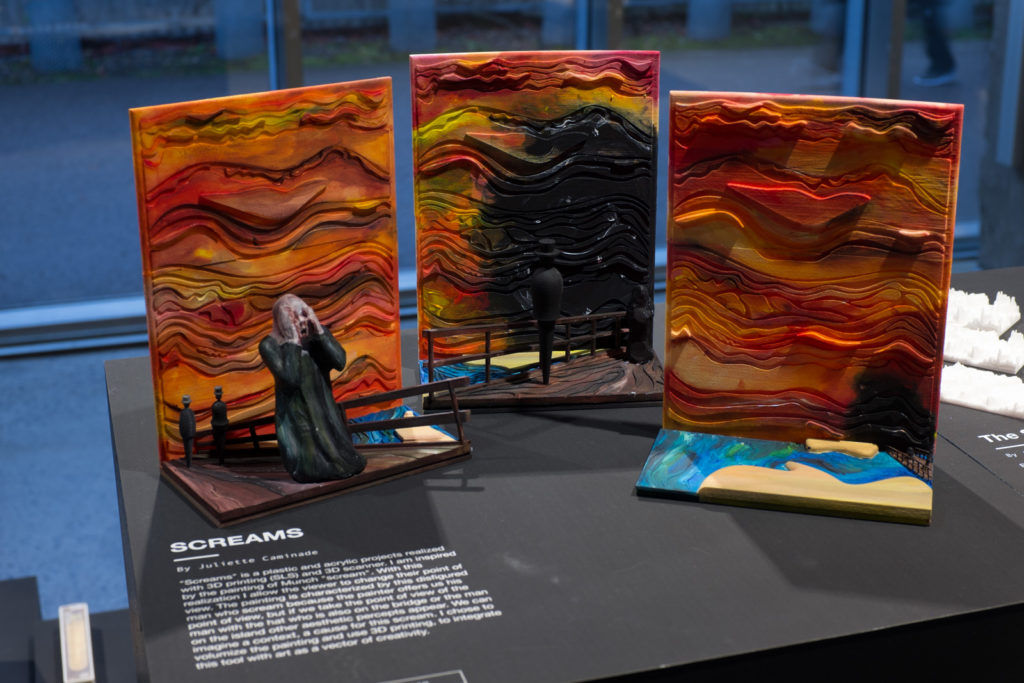
Juliette Caminade – Screams
“Screams” is a plastic and acrylic projects realized with 3D printing (SLS) and 3D scanner. I am inspired by the painting of Munch “scream”. With this realization I allow the viewer to change their point of view. The painting is characterized by this disfigured man who scream because the painter offers us his point of view, but if we take the point of view of the man with the hat who is also on the bridge or the man on the island other aesthetic percepts appear. We can imagine a context, a cause for this scream. I chose to volumize the painting and use 3D printing, to integrate this tool with art as a vector of creativity.
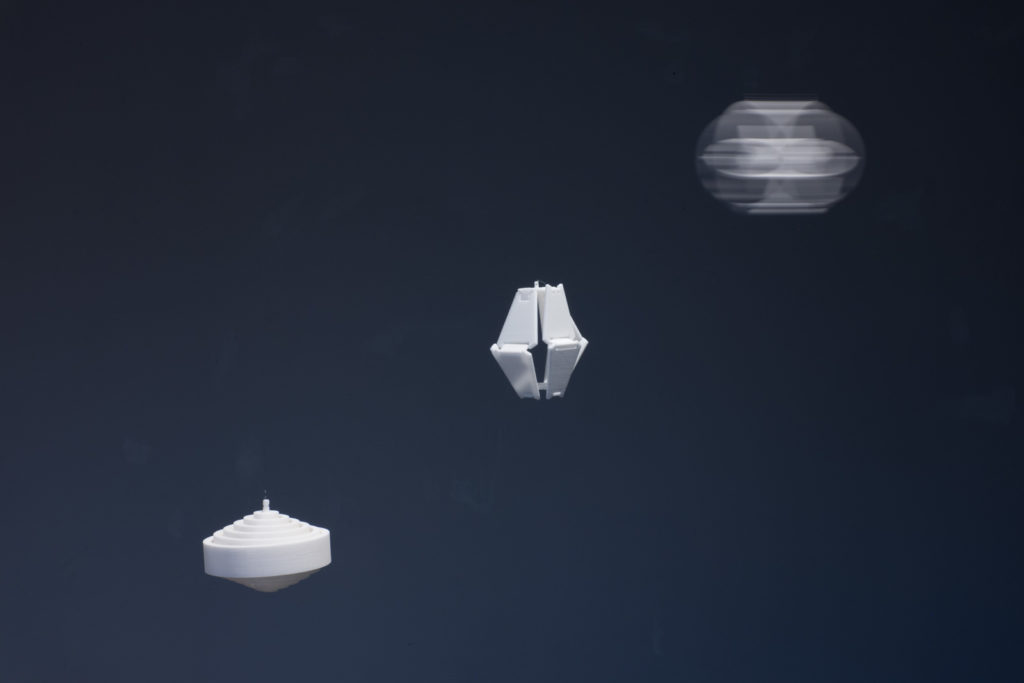
Emilie Langolf – Foldable ornaments
I have used joints, slots and axis to play with shape and function in order to make foldable ornaments. In this project i wanted to see how i could use movable parts with different principals to recreate traditional christmas tree ornaments. By using the SLS printer and comblining it with the looks of christmas ornaments i have made the decorations more flexible and compact compared to the original ornaments. They will take up less space when they are stored and are playful to fold out.

Ørjan Olav Johannesen – Deconstructing a Classic – Louis Poulsen PH-5
Challenging a modern classic by applying a postmodern deconstructive architectural principle to it. How can the lamp be rearranged, changing it’s qualities and intentions by distorting the form and creating unpredictability with added fragmenting elements and new technology. The PH-5 was created out of a simple requirement in the late 50s. Early incandescent bulbs presented a very harsh light in a room, so a 5 shade system was created with a softer and even light distribution. Looking at the lamp you would originally not see the light source. Rearranging the lamp and combining it with a modern LED bulb changes how the light is distributed. The lamp has been deconstructed in an analog way by sketching and making cardboard templates. It has then been analyzed and redrawn while making new ways of reassembling it in its new form. The new fragmenting flat elements are laser cut from 1,5mm acrylic. Joints are 3D printed in a ordinary FDM printer(Ultimaker).